Awesome Things You Can Learn From Studying Ultrasonic Receivers, Transmitters
Ultrasonic Receivers, Transmitters are explicitly designed to detect and transmit high-frequency waves. They are mainly characterized by three things that are frequency, rated voltage, and beam angle. Their operating frequency range varies, including 50Hz, 10kHz to 65kHz, 20kHz, 25kHz, 28kHz, 38kHz to 42kHz, 40kHz, and 42kHz, respectively 49.5kHz, 58kHz, 60kHz, 300kHz, 1MHz, 2.45mHz, and 168MHz.
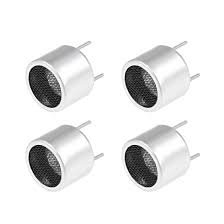
Ultrasonic Receivers
Ultrasonic Receivers, Transmitters have the flexibility and diverse capabilities that make up a large part of the proximity market and have continued to become even more popular over decades. The demand for ultrasonic receivers and transmitters has increased because of their use in robots, drones, autonomous vehicles, etc.
Advantages of Ultrasonic Receivers
- They are not affected by the colour, or finish of the items being detected
- They have flexible ranges in which the minimum range is down to a few centimeters and the maximum range up to around 5 centimeters.
- Ultrasonic receivers from the automation and control gear category have quick refresh rates and can make multiple measurements every second.
- These receivers are not expensive because of their basic building materials.
- The technology used is mature and developed, due to which you can understand them very well with predictable results.
- They are exact, with an error rate of only 1%.
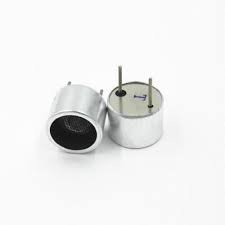
Ultrasonic Transmitters
An ultrasonic transmitter is usually mounted on the top of the tank and transfers an ultrasonic pulse down the tank. This pulse travels with the speed of sound and reflects the transmitter from the liquid surface. The transmitter then effectively measures the time delay between the transmitted and received signals. The onboard microprocessor is used to calculate the distance left to the liquid surface with the help of a formula.
Advantages of Ultrasonic Transmitters
- Ultrasonic transmitters are easy to install on empty tanks or tanks that usually contain some liquid.
- Set-up is very simple, and you can configure the devices with onboard programming capability in minutes.
- These automation and control gear components do not have any moving parts or contact with the media. Therefore, they are virtually maintenance-free. The wetted materials are commonly fluoropolymer and are highly resistant to corrosion from condensing vapours.
- These transmitters are non-contact, meaning the level measurement stays unaffected by changes in the liquid density, viscosity, or dielectric and performs very well in aqueous liquids and various chemicals.
- Changes in the process temperature can change the speed of the ultrasonic pulse through the space present above the liquid. However, built-in compensation can automatically fix this.
- The changes that take place in process pressure do not affect the measurement.
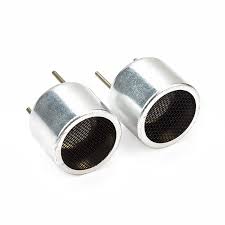
Applications of Ultrasonic Receivers
- The most common applications of Ultrasonic Receivers, Transmitters are automotive and industrial, but they also have many other applications.
- Ultrasonic sensors can detect transparent materials, often used for liquid-level sensing. This can be beneficial for the liquids that need to retain their purity or are toxic because these sensors are non-contact.
Another application is object detection which can be utilized in many industries, including manufacturing facilities, to detect boxes, vehicles, people, pallets, etc. The creativity of the design can also limit the applications of such sensors and transducers.